Perforated aluminum panels are widely used in architectural decoration, industrial applications, and home design due to their aesthetic appeal and practical functionality. The following is an overview of the perforated aluminum panel manufacturing process, from raw materials to finished products.
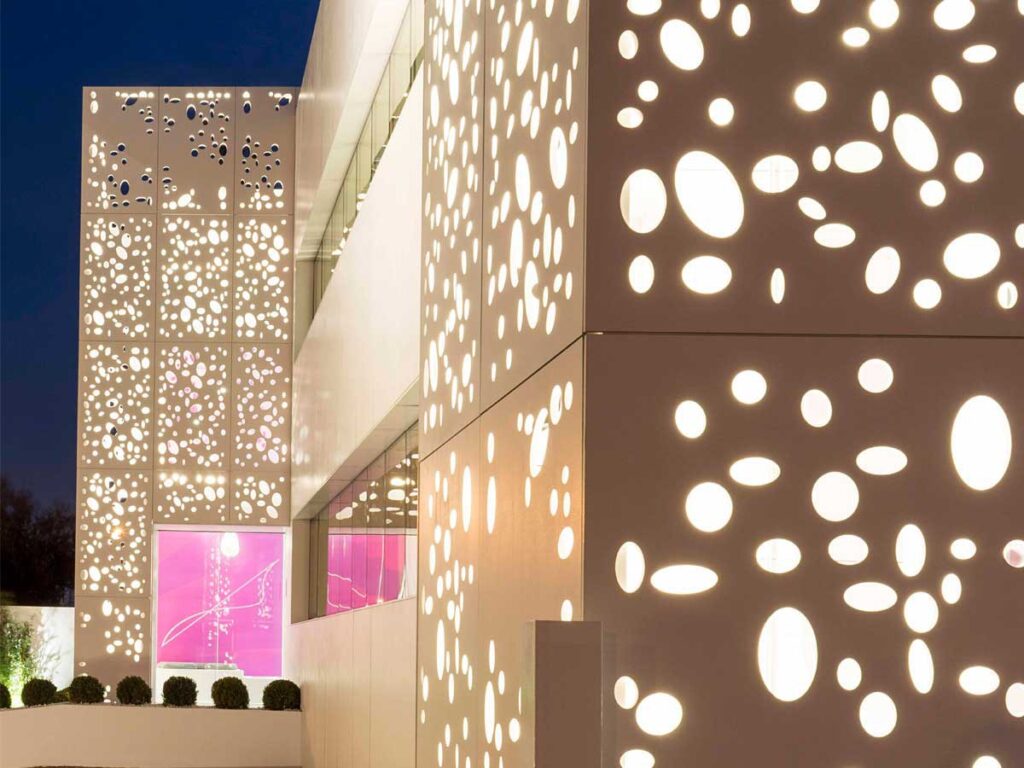
1. Raw Material Preparation
The first step in manufacturing perforated aluminum panels is selecting the appropriate aluminum sheet. Common materials include pure aluminum and aluminum alloys such as 3003 and 5052 alloys. Depending on the final product requirements, aluminum sheets of different thicknesses, hardness, and alloy compositions are chosen. Common thicknesses range from 1mm to 5mm.
2. Aluminum Sheet Cutting
Before perforation, the aluminum sheet needs to be cut according to the design specifications. Several cutting methods can be used:
- Shearing Machine: Suitable for cutting regular sizes.
- Laser Cutting Machine: Ideal for precision cutting of complex shapes, ensuring smooth and clean edges.
The cut aluminum sheets must remain flat for subsequent processing.
3. Perforation Process
Perforation is the key step in manufacturing perforated aluminum panels, typically carried out using a CNC punching machine. The punching machine creates holes in the aluminum sheet according to pre-set designs, including hole patterns and spacing. Common perforation types include:
- Round Holes: The most common hole shape, suitable for various applications.
- Square or Rectangular Holes: Used for specific design requirements.
- Custom-Shaped Holes: Custom shapes such as triangles or hexagons can be created as needed.
The perforation process includes:
- Setting the Mold: Select the appropriate mold based on the desired hole pattern and shape.
- Fixing the Aluminum Sheet: Secure the sheet on the punching platform to prevent movement during perforation.
- Punching Operation: The CNC machine automatically perforates the sheet according to the programmed settings, ensuring precise hole size, shape, and spacing.
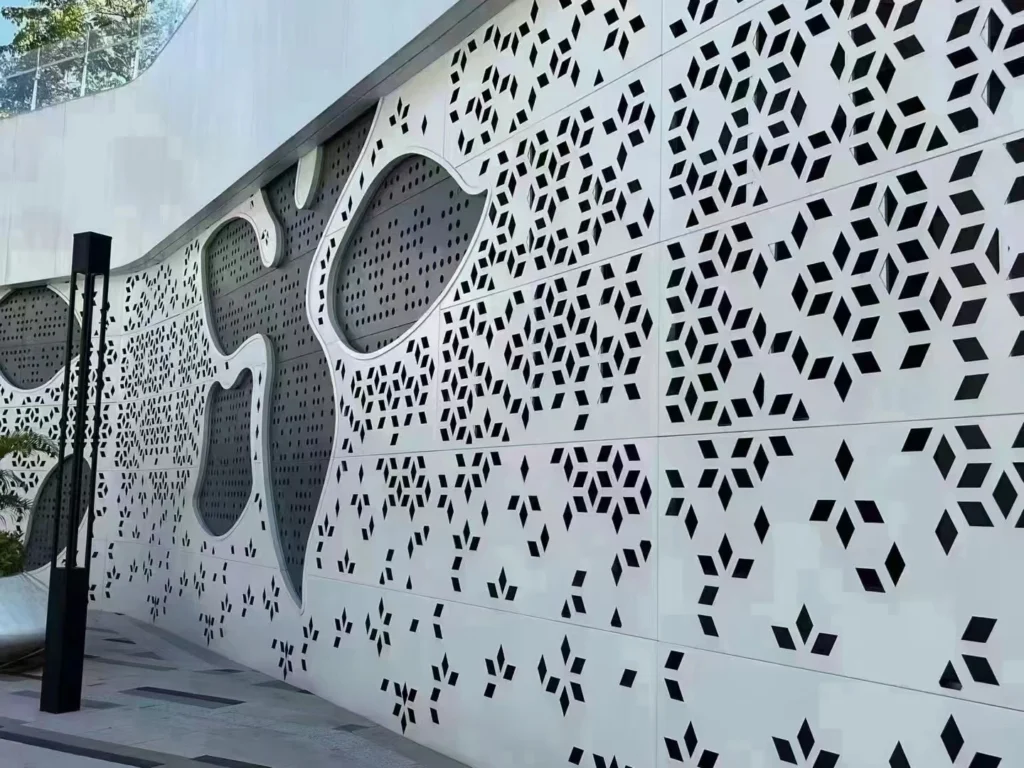
4. Edge Treatment
After perforation, the edges of the aluminum panel may have burrs or rough areas. To ensure a smooth and polished finish, the following treatments are applied:
- Grinding: A grinding machine is used to remove burrs and smooth the edges of the holes and the panel surface.
- Deburring: For panels with densely arranged small holes, deburring ensures that the hole edges are clean and neat.
5. Surface Treatment
To enhance corrosion resistance and improve aesthetics, perforated aluminum panels often undergo surface treatments. Common methods include:
- Anodizing: This electrochemical process forms a protective oxide layer on the aluminum surface, improving corrosion resistance and adding various color options.
- Powder Coating: Powder coating involves electrostatically spraying powder paint onto the aluminum surface, then baking it at high temperatures to form a durable coating. This method offers a wide range of color and texture choices.
- PVDF Coating (Fluorocarbon Coating): PVDF coatings provide excellent weather resistance and UV protection, making them ideal for exterior perforated aluminum curtain walls.
6. Final Inspection and Packaging
After surface treatment, the panels undergo a final quality inspection to ensure:
- The hole size, spacing, and pattern are accurate.
- The surface treatment is uniform, with no color differences or scratches.
- There are no burrs or other defects.
Once the panels pass inspection, they are packaged according to customer requirements. Protective packaging materials, such as bubble wrap or padding, are used to prevent scratches or damage during transportation.
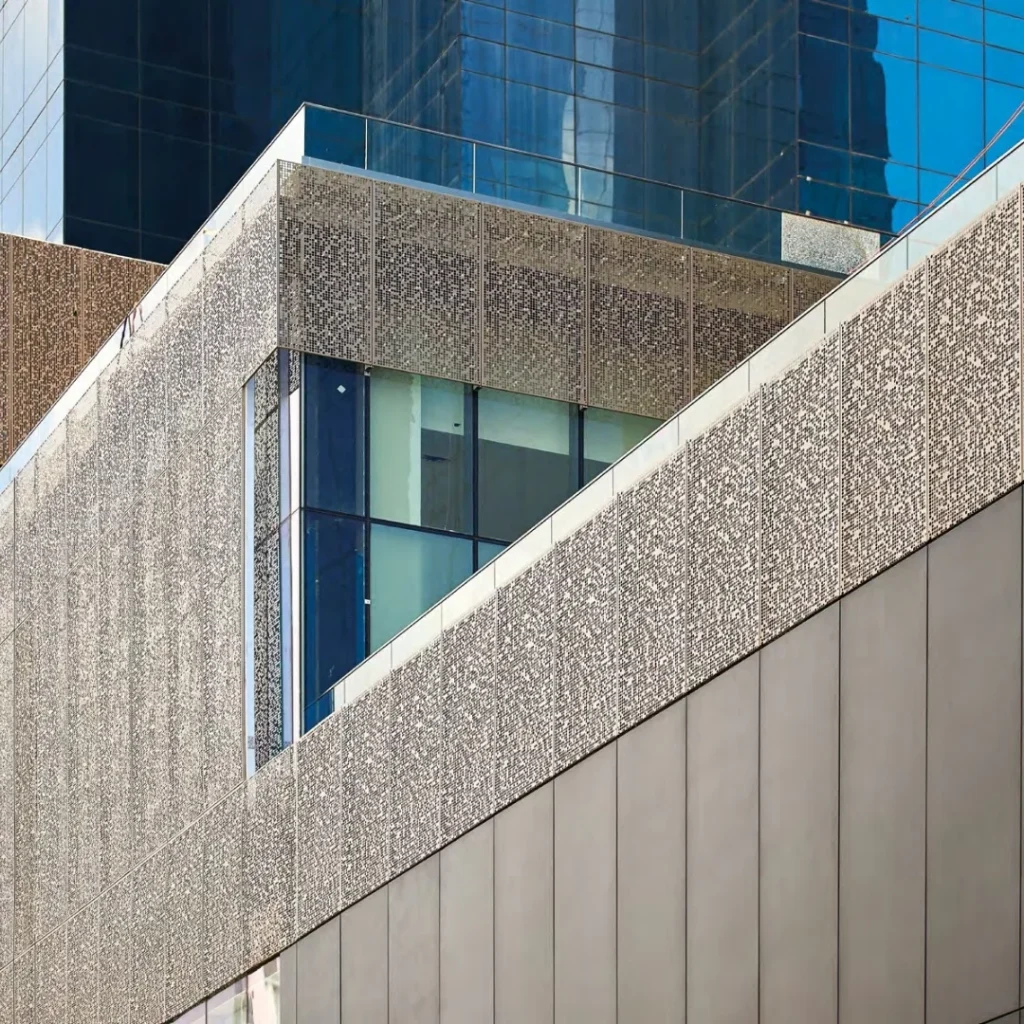
7. Installation and Applications
The final perforated aluminum panels can be used in various applications, such as building exterior decoration, ceilings, soundproof walls, curtain walls, and industrial ventilation systems. During installation, precise alignment and secure mounting according to design blueprints ensure a beautiful and stable finished product.
The manufacturing process for perforated aluminum panels combines modern equipment with strict quality control, ensuring both functionality and aesthetic appeal. These panels can also be customized to meet specific design needs. If you have any specific questions or need more detailed information, feel free to reach out!