Aluminum curtain wall panels are widely used in architectural decoration due to their lightweight, high strength, and corrosion resistance. To enhance their aesthetics and durability, these panels typically undergo surface treatments. Here’s an overview of the common surface treatment processes for aluminum curtain wall panels.
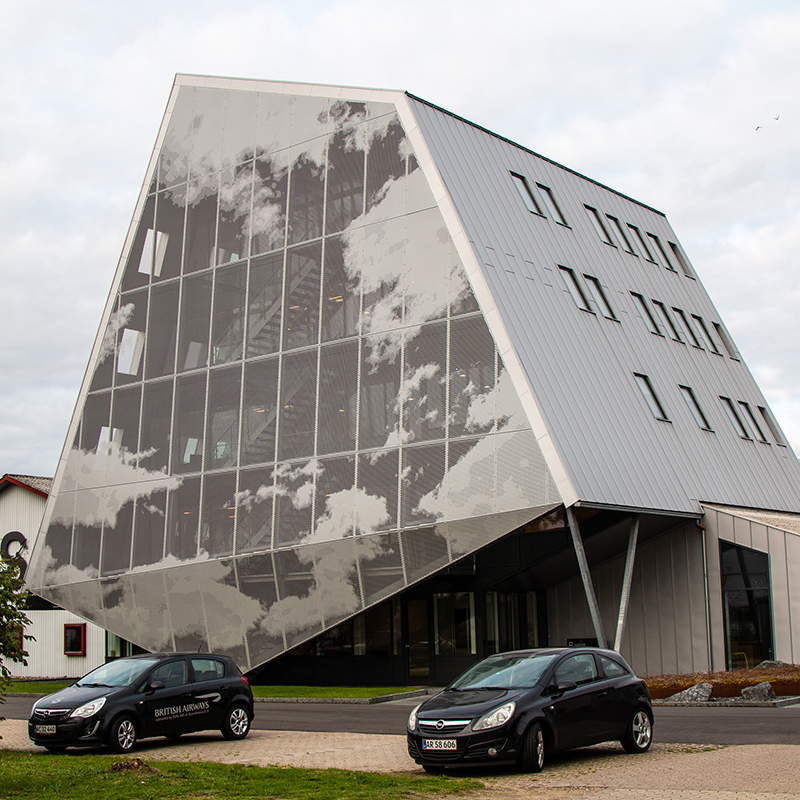
1. Anodizing
Anodizing is an electrochemical process that forms a protective oxide layer on the aluminum panel surface. The process includes cleaning, anodizing, electrolytic coloring, and sealing.
Advantages:
- Enhances corrosion resistance, effectively protecting the panel from moisture and acidic or alkaline environments.
- Allows for various colors, such as black, gold, bronze, and more.
- Increases surface hardness, making the panel more scratch-resistant and durable.
Applications: Primarily used for high-end interior and exterior wall decorations, where color and texture are essential.
2. PVDF Coating (Fluorocarbon Coating)
PVDF coating (polyvinylidene fluoride) is a spray coating process known for its excellent UV resistance, weatherability, and corrosion resistance. The coating includes a base coat, color coat, and clear coat, which are baked at high temperatures to form a solid protective layer.
Advantages:
- Excellent weather resistance, able to withstand sunlight, acid rain, and humidity, with a long service life.
- Color stability, resistant to fading and discoloration, making it ideal for long-term outdoor use.
- Smooth and easy-to-clean surface, suitable for large areas like curtain walls.
Applications: Widely used for exterior walls of high-rise buildings, commercial building facades, and large outdoor signage.
3. Powder Coating
Powder coating involves electrostatically applying powdered paint to the aluminum surface, followed by high-temperature baking to form a durable finish. This eco-friendly process is solvent-free.
Advantages:
- Thick, durable coating with strong adhesion, wear, and scratch resistance.
- Offers a variety of colors and textures, such as matte, glossy, and sand textures.
- Environmentally friendly and meets pollution control standards.
Applications: Ideal for indoor decoration, commercial wall cladding, and certain industrial uses.
4. Electrophoretic Coating
Electrophoretic coating deposits charged paint particles onto the aluminum panel through an electric current, creating a uniform, smooth finish. This process provides a thinner coating with excellent corrosion resistance and aesthetic appeal.
Advantages:
- High gloss, bright colors, and fine texture.
- High uniformity, suitable for complex shapes and small details.
- Strong coating, effectively preventing oxidation and corrosion.
Applications: Commonly used for building decorations, windows, railings, and other applications that require high surface gloss and uniformity.
5. Brushed Finish
Brushed finish is achieved by mechanically polishing the aluminum surface to create uniform lines, giving the panel a unique metallic texture. Brushed finishes can vary from coarse to fine, allowing for different visual effects.
Advantages:
- Improves fingerprint and scratch resistance.
- Strong metallic appearance, suitable for modern and high-tech architectural styles.
- Offers various patterns, such as straight grain, random grain, and spiral grain.
Applications: Often used in office buildings, modern-style commercial buildings, and interior walls that require a strong metallic texture.
6. Nano Self-Cleaning Coating
Nano self-cleaning coating is an emerging eco-friendly surface treatment technology. Nano materials form a super-hydrophobic film on the aluminum surface, effectively reducing dust and dirt adhesion.
Advantages:
- Self-cleaning properties reduce maintenance and cleaning costs.
- Environmentally safe and non-toxic.
- Waterproof and stain-resistant, keeping the panel looking new over time.
Applications: Suitable for high-rise building exteriors and hard-to-clean decorative walls.
These surface treatment processes for aluminum curtain wall panels each offer unique advantages, catering to a variety of application needs. When selecting the appropriate surface treatment, consider the building’s style, environmental conditions, and desired aesthetic effects. Feel free to reach out for more information or project-specific recommendations!